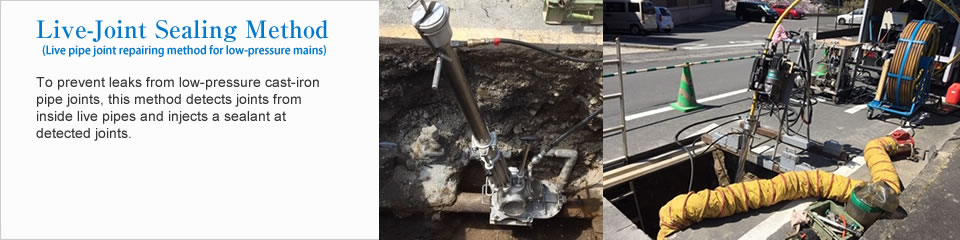
The live-joint sealing method is a system that detects joints from inside live (gas flowing) pipes and injects a sealant at detected joints to prevent leaks from low-pressure cast-iron pipe joints.
- (1) Applicable to: low-pressure cast-iron pipes 75 mm to 300 mm in dia.
(with spigot/gas pipe joints) - (2) Length: 30 to 50 m/side/pit
- (3) Bends: passage up to four 45o bends on one side
A hole of half the pipe diameter in diameter is bored in a low-pressure main. A packer is placed into the pipe under no blow conditions (no gas escaping) to detect joints. City gas of an increased pressure is used to inflate the packer, thereby injecting a sealant into the yarn in the joint clearance. Providing sealing this way, the live-joint sealing method prevents leaks from joints.
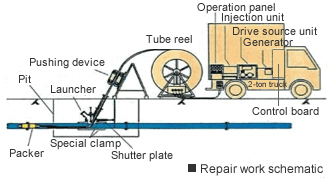
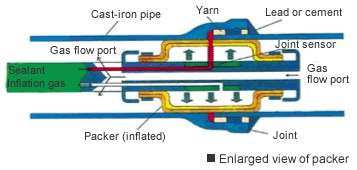
- (1) Repair work under no-blow live pipe conditions
- (2) Places a packer in the pipe through a small hole
- (3) Stops the packer at a joint with the combined use of a joint sensor with the system
- (4) Use of city gas to inflate the packer ensures safety even if the packer breaks
- (5) Measures the gas pressure at both ends of the packer to counter the problem of a decrease in gas pressure
- (1) Reduced repair work cost
Prevents leaks at 10% to 20% of the cost of conventional rehabilitation methods. - (2) Live pipe repair work
Provides improved customer service since the customer does not need to stop using gas.
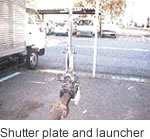
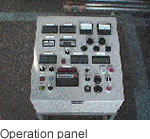
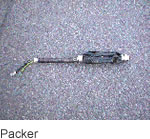
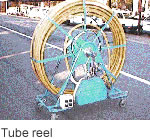
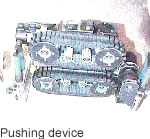
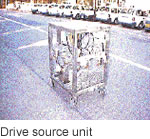